in a bustling factory in Ohio, a quality control manager named Sarah faced a daunting challenge: ensuring every product met the highest standards. One day, she discovered an AI tool that could analyze defects in real-time. Intrigued, she implemented it alongside her team. The AI quickly identified patterns in defects, allowing them to address issues before they escalated. Within weeks, product quality soared, and customer satisfaction followed suit. Sarah realized that with AI as her ally, quality control transformed from a tedious task into a streamlined, efficient process.
table of Contents
- Harnessing Machine Learning for Predictive Quality Insights
- Integrating AI-Powered Automation in Quality Control Processes
- Enhancing Data Analysis with AI for Real-Time Quality Monitoring
- Fostering a Culture of Continuous Improvement through AI Feedback Loops
- Q&A
Harnessing Machine Learning for Predictive Quality Insights
In the realm of quality control, machine learning has emerged as a transformative force, enabling organizations to anticipate and mitigate potential issues before they escalate. By leveraging vast amounts of past data, machine learning algorithms can identify patterns and anomalies that may not be instantly apparent to human analysts. This predictive capability allows companies to shift from reactive quality control measures to proactive strategies, ultimately enhancing product reliability and customer satisfaction.
One of the key advantages of employing machine learning in quality control is its ability to process and analyze data at an unprecedented scale. With the integration of sensors and IoT devices, manufacturers can collect real-time data from production lines, which can then be fed into machine learning models. These models can analyze variables such as temperature, humidity, and machine performance to predict potential defects. As a result, organizations can implement corrective actions swiftly, reducing waste and minimizing downtime.
Moreover, machine learning can facilitate continuous improvement by providing insights into the root causes of quality issues. By utilizing techniques such as clustering and classification, businesses can categorize defects and identify common factors contributing to quality failures. This data-driven approach empowers teams to make informed decisions about process adjustments, training needs, and equipment upgrades. Consequently, organizations can foster a culture of quality that is both proactive and responsive.
the integration of machine learning into quality control processes can enhance collaboration across departments. By sharing predictive insights with teams in production, engineering, and supply chain management, organizations can create a unified approach to quality assurance. This collaborative environment not only streamlines interaction but also ensures that all stakeholders are aligned in their commitment to maintaining high standards. ultimately, harnessing the power of machine learning can lead to a more resilient and efficient quality control framework.
Integrating AI-powered Automation in Quality Control Processes
Incorporating AI-powered automation into quality control processes can revolutionize how businesses maintain product standards. By leveraging machine learning algorithms, companies can analyze vast amounts of data in real-time, identifying patterns and anomalies that human inspectors might overlook. This not only enhances the accuracy of quality assessments but also substantially reduces the time required for inspections, allowing for faster production cycles.
One of the most effective applications of AI in quality control is through the use of computer vision technology. This allows for automated visual inspections, where cameras equipped with AI can detect defects in products with remarkable precision. For instance, in manufacturing sectors such as automotive or electronics, AI systems can quickly assess components for flaws, ensuring that only products meeting stringent quality standards reach the market. This capability not only minimizes human error but also provides a consistent level of scrutiny across all production batches.
Moreover, AI can facilitate predictive maintenance, which is crucial for maintaining quality control in production environments. By analyzing data from machinery and equipment, AI systems can predict when a machine is likely to fail or produce subpar products. This proactive approach enables companies to address potential issues before they escalate, thereby maintaining high-quality output and reducing downtime. Implementing such systems can lead to significant cost savings and improved operational efficiency.
integrating AI into quality control processes fosters a culture of continuous improvement. With AI-driven analytics, businesses can gather insights into their production processes, identifying areas for enhancement. This data-driven approach empowers teams to make informed decisions,optimize workflows,and implement best practices. As a result, organizations can not only uphold quality standards but also innovate and adapt to changing market demands more effectively.
Enhancing Data Analysis with AI for Real-Time Quality Monitoring
In the fast-paced world of manufacturing and production, the ability to monitor quality in real-time is crucial for maintaining standards and ensuring customer satisfaction.By integrating AI technologies into quality control processes, companies can leverage advanced algorithms to analyze data streams from various sources, such as sensors and production lines. This not only enhances the speed of data analysis but also improves accuracy, allowing for immediate identification of potential quality issues.
AI-driven systems can process vast amounts of data at lightning speed,enabling organizations to detect anomalies that may indicate defects or deviations from quality standards. These systems utilize machine learning models that continuously learn from historical data, adapting to new patterns and trends.As a result, businesses can implement proactive measures to address quality concerns before they escalate, reducing waste and minimizing costly recalls.
Moreover, the integration of AI in quality monitoring facilitates a more comprehensive understanding of the production process. By employing predictive analytics, companies can forecast potential quality issues based on real-time data, leading to informed decision-making. This approach not only enhances operational efficiency but also fosters a culture of continuous improvement, as teams can focus on refining processes based on actionable insights derived from AI analysis.
To maximize the benefits of AI in quality control, organizations should consider the following strategies:
- invest in robust data infrastructure: Ensure that data collection systems are capable of capturing high-quality, real-time data from all relevant sources.
- Train staff on AI tools: Equip employees with the necessary skills to interpret AI-generated insights and integrate them into their daily workflows.
- Foster collaboration: Encourage cross-departmental collaboration to share insights and drive a unified approach to quality management.
- Continuously evaluate AI performance: Regularly assess the effectiveness of AI systems and make adjustments as needed to enhance their accuracy and reliability.
Fostering a Culture of continuous Improvement through AI Feedback Loops
Incorporating AI feedback loops into quality control processes can significantly enhance the ability of organizations to identify and rectify issues in real-time. By leveraging machine learning algorithms, companies can analyze vast amounts of data generated during production, allowing for a more nuanced understanding of quality metrics. This data-driven approach not only highlights areas needing improvement but also provides actionable insights that can be implemented swiftly, fostering a proactive rather than reactive quality control environment.
One of the key advantages of AI feedback loops is their capacity to learn from past mistakes. As the system processes historical data, it can identify patterns and correlations that may not be immediately apparent to human analysts. This capability enables organizations to establish **predictive maintenance schedules**, ensuring that equipment is serviced before failures occur, thus minimizing downtime and maintaining product quality. Additionally, by continuously refining its algorithms, AI can adapt to new challenges and evolving production standards, ensuring that quality control measures remain relevant and effective.
Moreover, integrating AI into quality control encourages a culture of collaboration across departments. When teams have access to real-time data and insights, they can work together more effectively to address quality issues.For instance, production teams can communicate directly with quality assurance personnel, sharing feedback and observations that can be analyzed by AI systems. this collaborative approach not only enhances the quality of the final product but also empowers employees to take ownership of their roles in the quality control process.
requires a commitment to ongoing training and development. Organizations should invest in upskilling their workforce to ensure that employees are equipped to interpret AI-generated insights and implement changes accordingly. By creating an environment where learning is prioritized, companies can cultivate a mindset that embraces innovation and improvement, ultimately leading to higher quality standards and increased customer satisfaction.
Q&A
-
What is AI in quality control?
AI in quality control refers to the use of artificial intelligence technologies, such as machine learning and computer vision, to enhance the processes of monitoring and ensuring product quality. It helps in identifying defects, predicting failures, and optimizing production processes.
-
How can AI improve defect detection?
AI can improve defect detection by analyzing images and data from production lines in real-time. Using algorithms, it can identify patterns and anomalies that may indicate defects, frequently enough with greater accuracy and speed than human inspectors.
-
What are the benefits of using AI for predictive maintenance?
Using AI for predictive maintenance allows companies to:
- Reduce downtime by predicting equipment failures before they occur.
- Optimize maintenance schedules based on actual equipment condition rather than fixed intervals.
- Lower maintenance costs by addressing issues proactively.
-
How can small businesses implement AI in quality control?
Small businesses can implement AI in quality control by:
- Starting with pilot projects that focus on specific quality issues.
- Utilizing cloud-based AI solutions that require less upfront investment.
- Collaborating with technology partners or consultants to integrate AI tools into existing processes.
Incorporating AI into quality control not only enhances precision but also fosters innovation. As industries evolve, embracing these technologies will empower businesses to maintain high standards and stay competitive in the ever-changing market landscape.
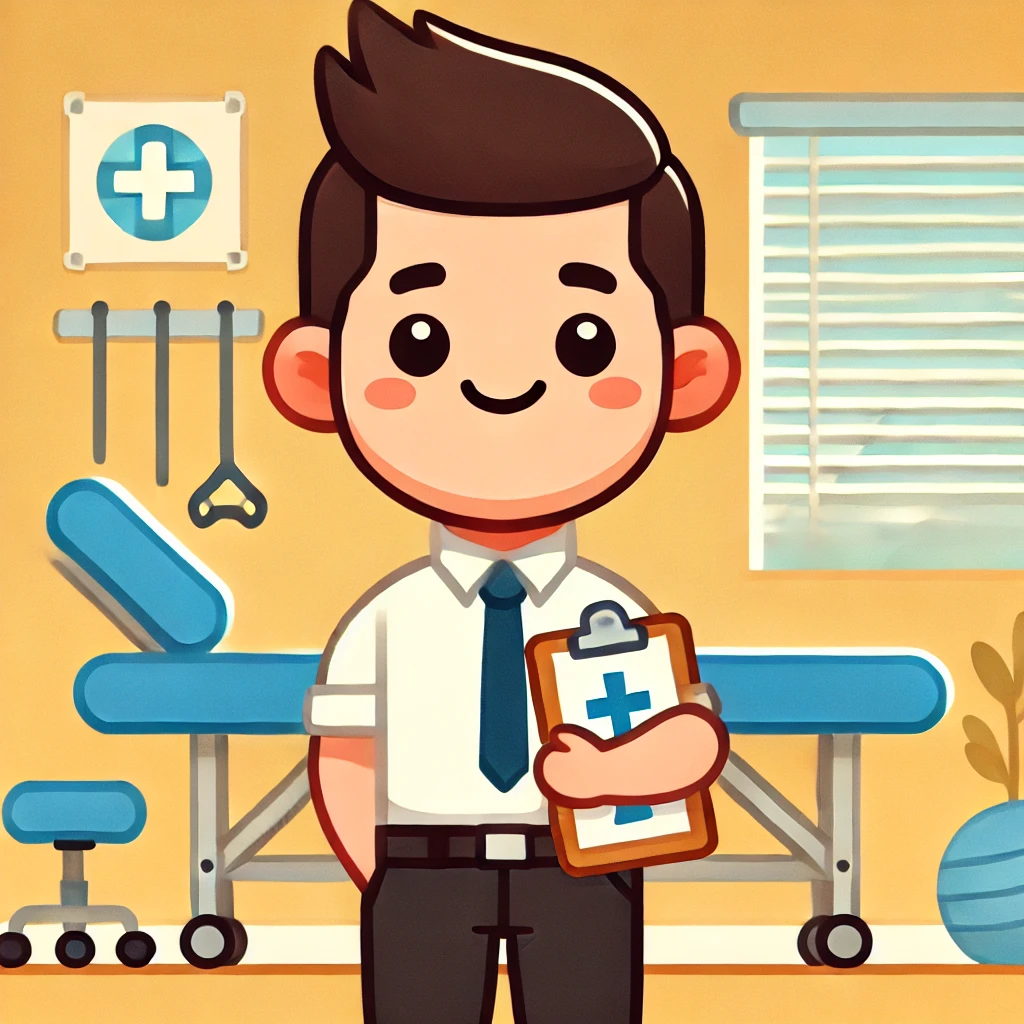